DRY ICE and dry ice cleaning
Dry ice cleaning is a COMPLETELY DRY and water-less process, which is an upgrade of traditional techniques and replaces blasting, high-pressure washing and steam cleaning.
Our dry ice cleaning services are used by:
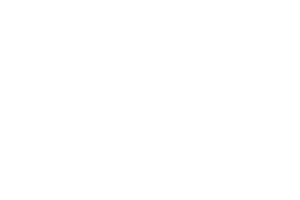
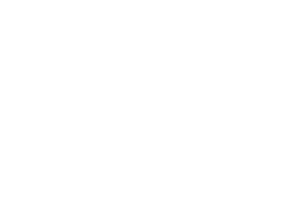
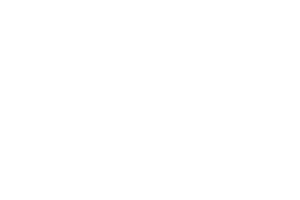
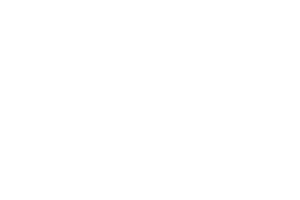
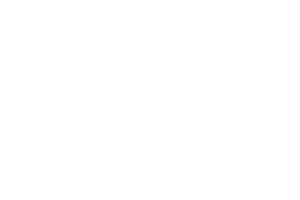
Dry ice cleaning
We perform professional cleaning of the most sensitive components of process equipment (production and packaging lines, electronics, electrical cabinets, installations, sensors, molds, tools, mixers…)!
Production is clean again without downtime and 80% faster
Use dry ice for the hardest to reach places without disassembling your equipment!
Advantages of dry ice cleaning
The machines can also be cleaned during operation, and they can be run immediately after the service is completed.
- No surface damage.
- Cleaning can be done during the production process.
- Suitable for work in HACCP environment.
- Suitable for cleaning sensitive surfaces (electronic circuits, sensors ...).
Why dry ice cleaning?
When it comes to stubborn dirt, burns or sensitive electronics, dry ice cleaning is the BEST option.
This technology does not contaminate the environment, and production can be run immediately after the cleaning. See: DRY ICE – BEST CASE STUDIES OF CLEANED SURFACES (click).
Working principle
This is a high-pressure cleaning process (up to 16 bar). Compressed air accelerates dry ice particles to supersonic speeds, meaning the particles strike the surface with high kinetic energy.
The surface freezes in an instant and microcracks are formed in the contaminant. The dry ice particles sublime away after impacting the surface, causing micro-explosions which blow the loosened dirt away from the surface.
Use cases by industry
Extend the life of your machines and devices! Use dry ice!
Click on one of the industries below to see the use cases.
Dry ice in the automotive industry
Use cases:
- cleaning of welding robots and welding tables
- cleaning of vapour incinerators
- conveyor chains and belts in painting and drying chambers
- cleaning of foundry tools (for grey cast iron and aluminium)
- cleaning of plastic and rubber injection molding tools
- heat exchangers (thermal wheels, heaters, refrigerators)
- electrical and communication cabinets (robot cabinets, locator cabinets, SOP, MOP)
Dry ice for the pharmaceutical industry
Use cases:
- cleaning of tablet presses and lines before changing the batch
- cleaning and maintenance of mechanical parts of lines
- cleaning conveyor belts and chains
- cleaning and maintenance of transport systems for bulk and liquid materials
- suitable for work in HACCP environments
- maintenance of machinery designed for Ex conditions
- maintenance of electronics in control systems and electrical cabinets
Dry ice for the chemical industry
Use cases:
- cleaning of furnaces and painting lines
- cleaning and restoration of mixers and tanks
- cleaning of mills, extruders and transport lines for various media
- maintenance of electronic components and control cabinets
- motors, drive parts and reduction gears
- chains and belts
- burns, all types of resins, soot, grease and similar contaminants are removed with high efficiency
Dry ice for the food industry
Use cases:
- cleaning of ovens and conveyor belts
- cleaning and restoration of mixers and tanks
- cleaning of mills, extruders and transport pipelines for various media
- general cleaning of filling and packaging lines
- cleaning moulds on the machine during the production of PET packaging
- maintenance of electronic components and control cabinets
- burns, caramelized sugar, grease, soot and other similar contamination is removed with high efficiency
- suitable for work in HACCP environments
Dry ice for the aerospace industry
Use cases:
- cleaning of jet engines
- cleaning and degreasing of vital mechanical aircraft assemblies
- cleaning at hard-to-access places (gaps, corners …)
- cleaning of landing gear and braking systems
- electronic components
- removing labels without damage to the base coating
- cleaning of runways and signal lighting
Dry ice for the electrical industry
Use cases:
- cleaning of generators, stators, rotors
- electrical cabinets
- high-voltage insulators
- turbine blades
- HRSG heat exchangers (Heat recovery steam generator)
- combustion chambers
- cleaning of pools and tanks for system cooling water
What do customers think?
“We wish to thank Blast Tehnik for suggesting us to use dry ice. We achieved immediate results and saved a lot of time and money. Our plastic injection moulding machines and moulds are now regularly impeccably clean. This allows us to ensure constant product quality and much easier tool maintenance.”
Simon Drofenik
Deplast d.o.o.
More than 30 years of experience
- 5 year warranty on our services.
- We are not stopping your production processes!
- We carry out the work according to European standards and requirements.
- We satisfy all quality requirements for the most demanding customers such as Groupe Renault, Novartis, Krka and others.
How do dry ice cleaning machines work?
Dry ice machines running on compressed air emit carbon dioxide pellets at supersonic speeds. As they strike the surface, these pellets/particles sublime away, removing dirt and contaminants. The surface thus remains dry and becomes impeccably clean without secondary waste.